Duraluminium
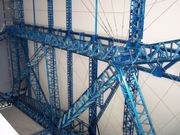
Duraluminium - eine Sammelbezeichnung für eine Gruppe hochfester Legierungen auf Aluminiumbasis (Aluminiumlegierung) mit Zusätzen von Kupfer , Magnesium und Mangan. Legierung Name kommt von der Marke Dural - Handelsbezeichnung eines der ersten aushärtbaren durch Wärmebehandlung und anschließende Alterung von Aluminiumlegierungen . Das Hauptlegierungselemente darin waren Kupfer (4,5% der Masse), Magnesium (1,5%) und Mangan (0,5%); der Rest ist Aluminium (93,5%). Beim Testen der Zugfestigkeit typischen Wertes der Streckgrenze ist Duraluminium etwa 250 MPa , eine Zugfestigkeit von 400 ... 500 MPa , aber die Festigkeitseigenschaften der jeweiligen Legierung hängen von ihrer Zusammensetzung , und insbesondere durch die Wärmebehandlung.
Duraluminium oder kurz Dural genannt, ist eine Aluminiumlegierung, die eine besonders hohe Festigkeit hat. Der Name stammt aus dem Lateinischen (durus=hart). Seine Legierung Al, 4% Cu, 0,7% Mn, 0,8% Mg wurde zum Patent angemeldet, der Name DURAL® ist geschützt.
Entwicklung
Es wurde 1906 von Dr.Alfred Wilm durch die erstmalige Anwendung der Ausscheidungshärtung bei Aluminiumlegierungen in seinem Laboratorium entwickelt. Die Entdeckung der Härtbarkeit von Aluminiumlegierungen erfolgte als Wilm versuchte, die in der Stahlherstellung gebräuchliche Verfahren auf Aluminiumlegierungen anzuwenden. Erst als er die Aluminiumproben einige Tage liegen ließ und danach Versuche anstellte, zeigte sich das erhoffte Resultat. Die Grundlage für die Härtung liegt darin, dass der Kupferanteil bei 500 °C, also in der Schmelze, vom Aluminium vollständig aufgelöst werden kann. Bei Raumtemperatur beträgt dieser Anteil nur 0,5%. Das außerordentlich harte CuAl2 bildet sich nur langsam. Diese intermetallische Verbindung sorgt aber letztlich dafür, dass sich Gefügeänderungen in der Legierung kaum ausbreiten kännen.
Materialeigenschaften
Duraluminium besteht aus etwa 93 bis 95 Prozent reinem Aluminium mit Zusatzen 3,5-5,5 Prozent Kupfer, sowie geringen Beigaben von Magnesium, Mangan und Silizium. Die Legierung wird auch heute noch fast unverändert in der Luftfahrt verwendet.
Gegenüber reinem Aluminium hat Duraluminium eine geringfügig größere Dichte. Die Zugfestigkeit beträgt jedoch 420-500 N/mm2 und damit etwa das 5-fache von reinem Aluminium, das nur etwa 80 N/mm2 aufweist. Ähnlich verhält es sich bei der Brinellhärte, wo ein HB-Wert von etwa 125 gegenüber 30 bei Reinaluminium erreicht wird. Die Bruchdehnung wird mit 22% als dreifach höherer Wert gegenüber 7% bei Reinaluminium angegeben. Ein weiterer wichtiger Punkt war, dass Duraluminium durch Alterung an seiner Festigkeit nichts einbüßte.
Vergleichstabelle Materialwerte | |||||
---|---|---|---|---|---|
Material | Spez. Gewicht / Dichte in kg/dm3 | E-Modul in N/mm2 | Zugfestigkeit in N/mm2 | Bruchdehnung in % | Brinellhärte HB |
Dural® Al95/Cu 4/Mg 1 | 2,75 - 2,87 | 73.000 | 420-500 | < 22 | 115-135 |
Reinaluminium Al99,5 | 2,7 | 70.000 | 75 - 110 | < 7 | 22 - 35 |
Stahl S355 | 7.9 | 200.000 | 510 | 19 | 120 - 140 |
V2A Chrom-Nickel-Stahl | 7.9 | 200.000 | 500 - 750 | 40 | 130 - 190 |
Durch das Aushärten erreicht Duraluminium also fast die Festigkeit von Stahl. Es ist allerdings korrosionsanfälliger als Reinaluminium, das im Normalfall durch eine natürliche Aluminiumoxidschicht geschützt wird. Dies kann durch einen Überzug aus reinem Aluminium (Handelsname: Alclad), Eloxieren und/oder Lackierung minimiert werden. Durch eine veränderte Legierungszusammensetzung unter Zugabe von Silikaten wurde aus dem Duralumin die wesentlich korrosionsfestere Legierung Silumin entwickelt, die im Motorenbau für Schiffe zum Einsatz kommt und erhöhte Korrosionsbeständigkeit gegen Seewasser aufweist.
Herstellung
Das Material wurde ab 1909 von den Dürener Metallwerken hergestellt und der Name Duraluminium als eingetragenes Warenzeichen geschützt. Avional, Hiduminium und andere Namen sind ähnliche Legierungen anderer Hersteller.
Anwendungen
Durch die verbesserten Materialeigenschaften wurde der Ersatz von Stahl durch eine Aluminiumlegierung in der Luftfahrt überhaupt sinnvoll. Frühere Legierungen (wie die Zink-Aluminium-Legierungen) waren korrosionsanfällig und erreichten bei weitem nicht die erforderliche Festigkeit.
Bereits 1911 fand Duraluminium eine großtechnische Anwendung für das Traggerüst des britischen Luftschiffes HMA No. 1 "Mayfly". Ab 1914 wurde es auch für den deutschen Zeppelinbau (erstmals bei den LZ 26 und / Z XII) eingesetzt. 1929 wurde ein Ganzmetall-Luftschiff, das amerikanische ZMC-2, vollständig, das heißt inklusive einer Blech-Gashülle aus Duraluminium gefertigt.
Neben den Luftschiffbauern wurde auch Hugo Junkers angeregt, Duraluminium bei der Junkers J.4 einzusetzen. Eines der ersten Passagierflugzeuge, die Junkers F 13, war ein Ganzmetall-Verkehrsflugzeug, bei dem Duralumin als Werkstoff für das Chassis verwendet wurde. Im modernen Flugzeugbau ist Duralumin heute als Werkstoff 2017, 2117 oder 2024 bekannt.
Der Einsatz im Kraftfahrzeugbau ist durch den hohen Preis nur eingeschränkt möglich. Es ist jedoch mittlerweile ziemlich gebräuchlich, wenn es besonders auf ein gutes Leistungsgewicht ankommt. Beispiele für den Einsatz sind Räder, Zylinderköpfesonders auf ein gutes Leistungsgewicht ankommt. Beispiele für den Einsatz sind Räder, Zylinderköpfe, Motorblöcke, Kurbelgehäuse, Ölwannen, Verteiler, Karosserie oder Karosserieteile, Rahmen, Stoßstange und Kraftstofftank, Gehäuse des Differenzialgetriebes, Motorhaube und Kofferraumklappe.
Duralumin ist auch beliebt für Präzisionswerkzeuge.

© biancahoegel.de;
Datum der letzten Änderung: Jena, den: 09.02. 2022